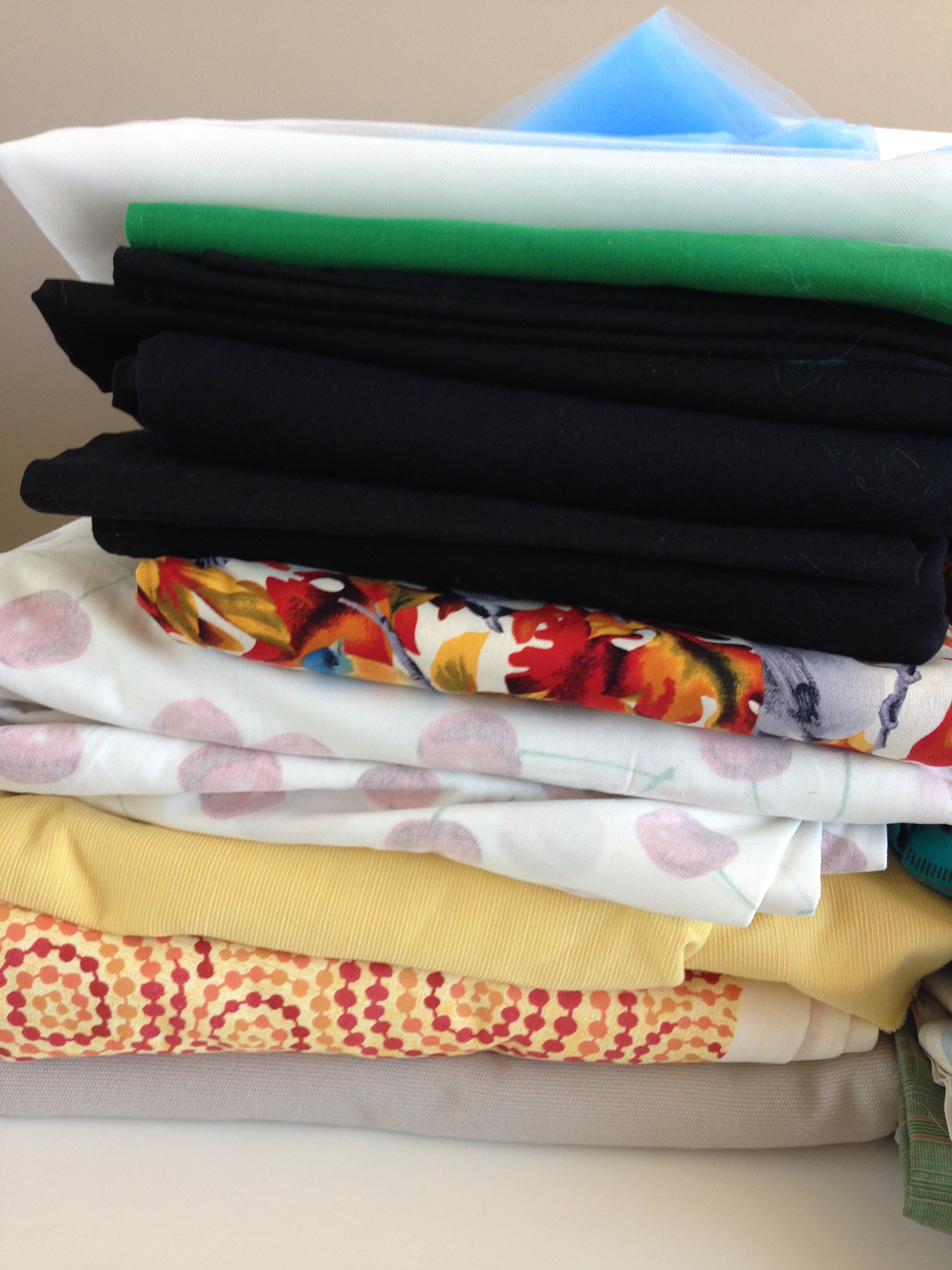



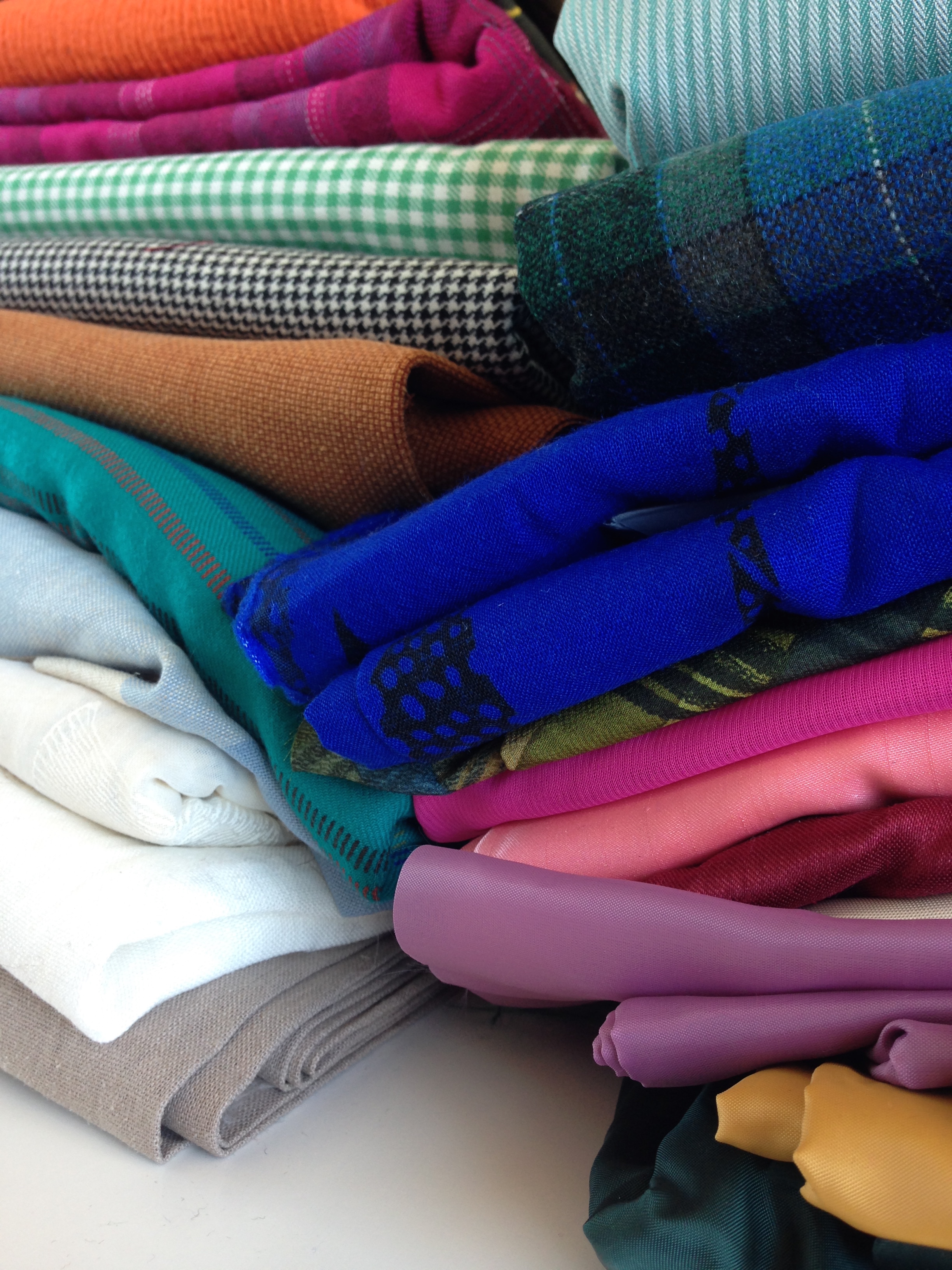
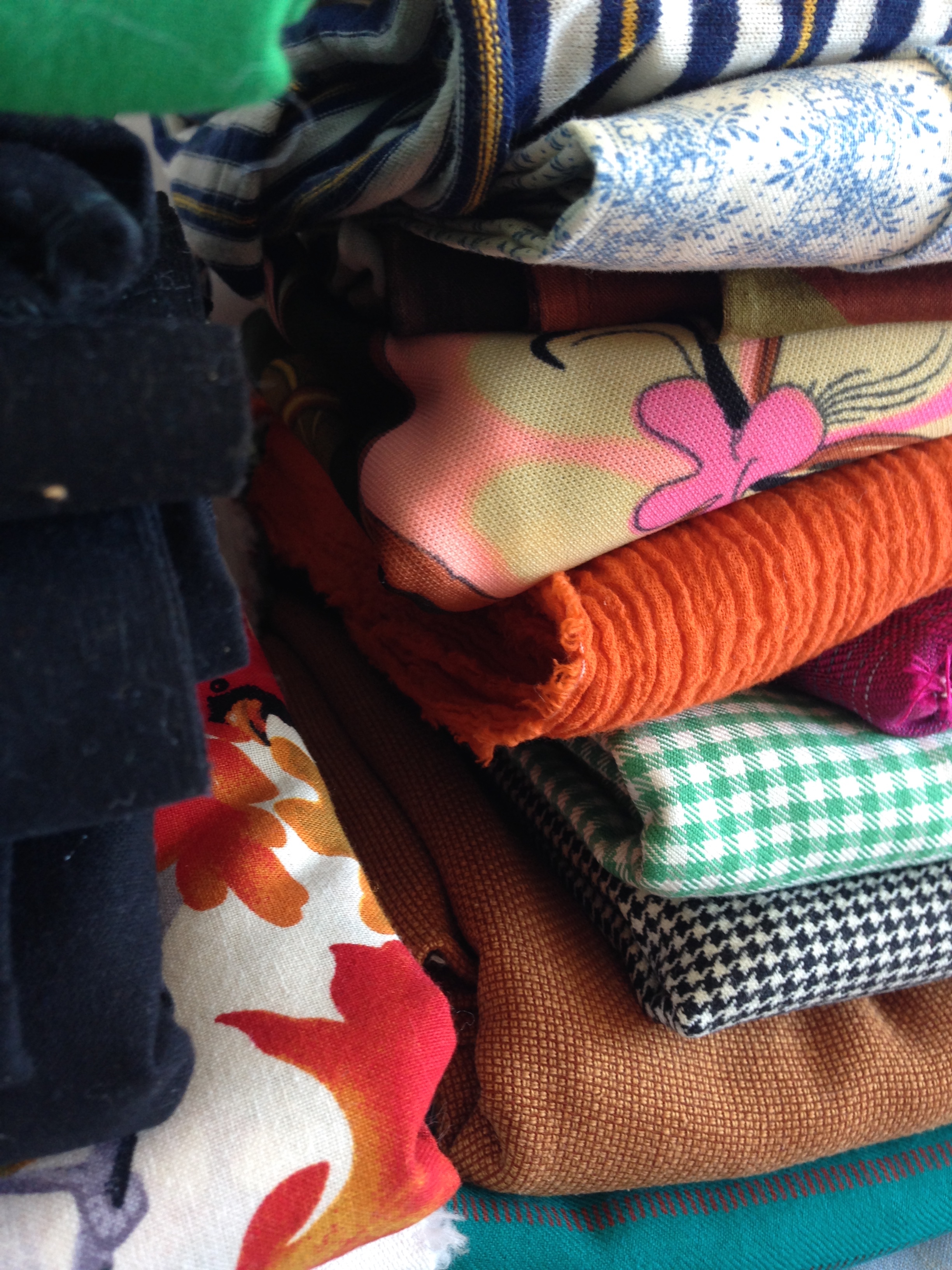
I will admit it. I've been a very bad sew-er lately. I haven't actually started a new project since beginning my upholstery project in 2014. I'm happy to say I've finished with the upholstery project though! Well, as finished as it's going to be, 2 out of 4 chairs is good enough, right? It's time for something new!
I'm not sure I've ever unearthed my fabric collection online before. It's not the most shameful thing... but it's pretty up there. Enough that I'm not allowed to go buy more.
While I was going through all the lovely wools and cotton prints, I found a wool green gingham complete with pattern and buttons, oh my! (Past Andrea had ambitions and present Andrea is going to take advantage.)
Anyways. Since the green wool gingham is perfect for this soon to be holiday dress. Cherry button included. So I got scheming with my lovely Lady Lesley and we set up a sewing skype date to hopefully get both our projects rolling.
Step one is always iron out that fabric flat.


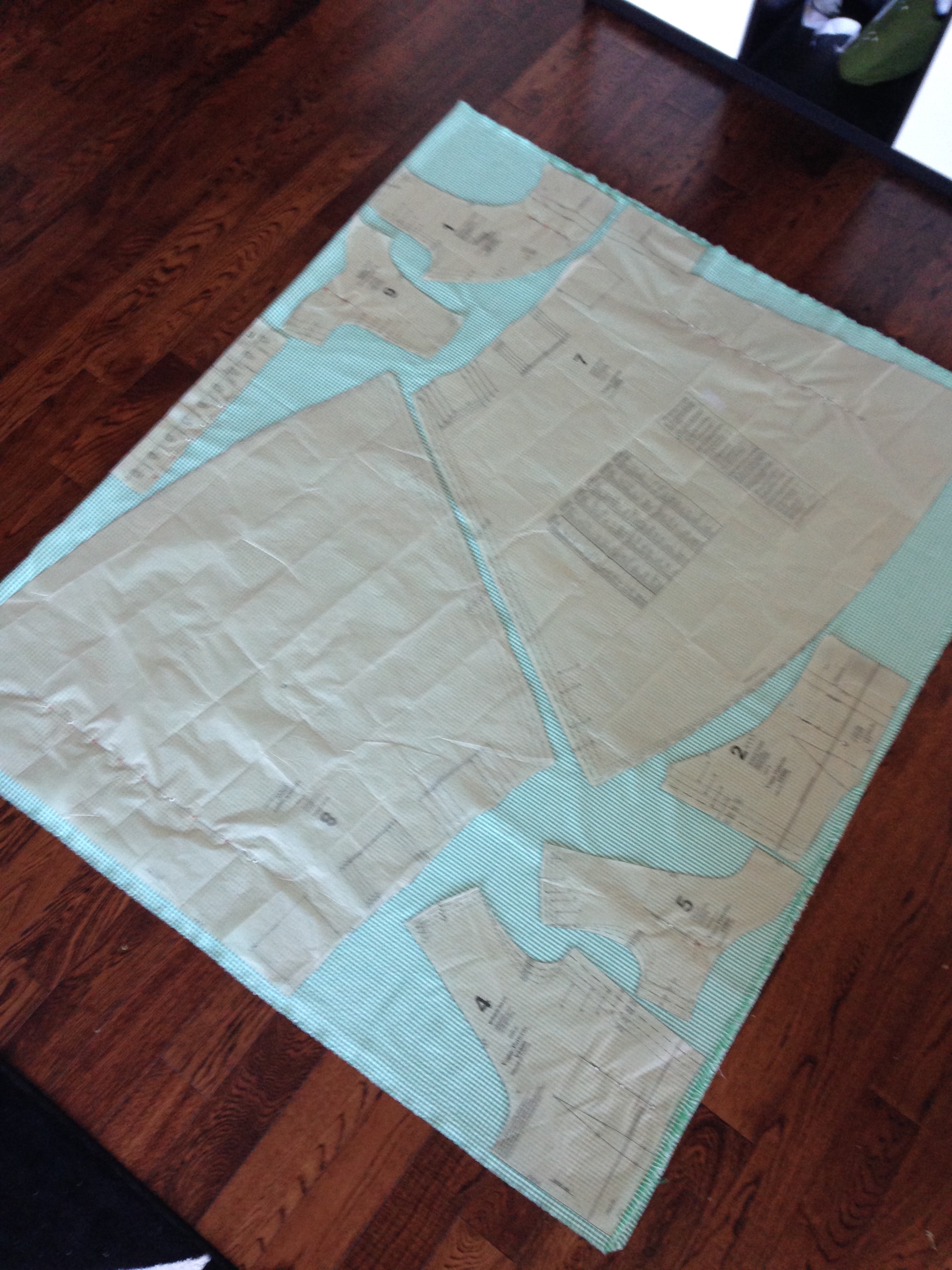
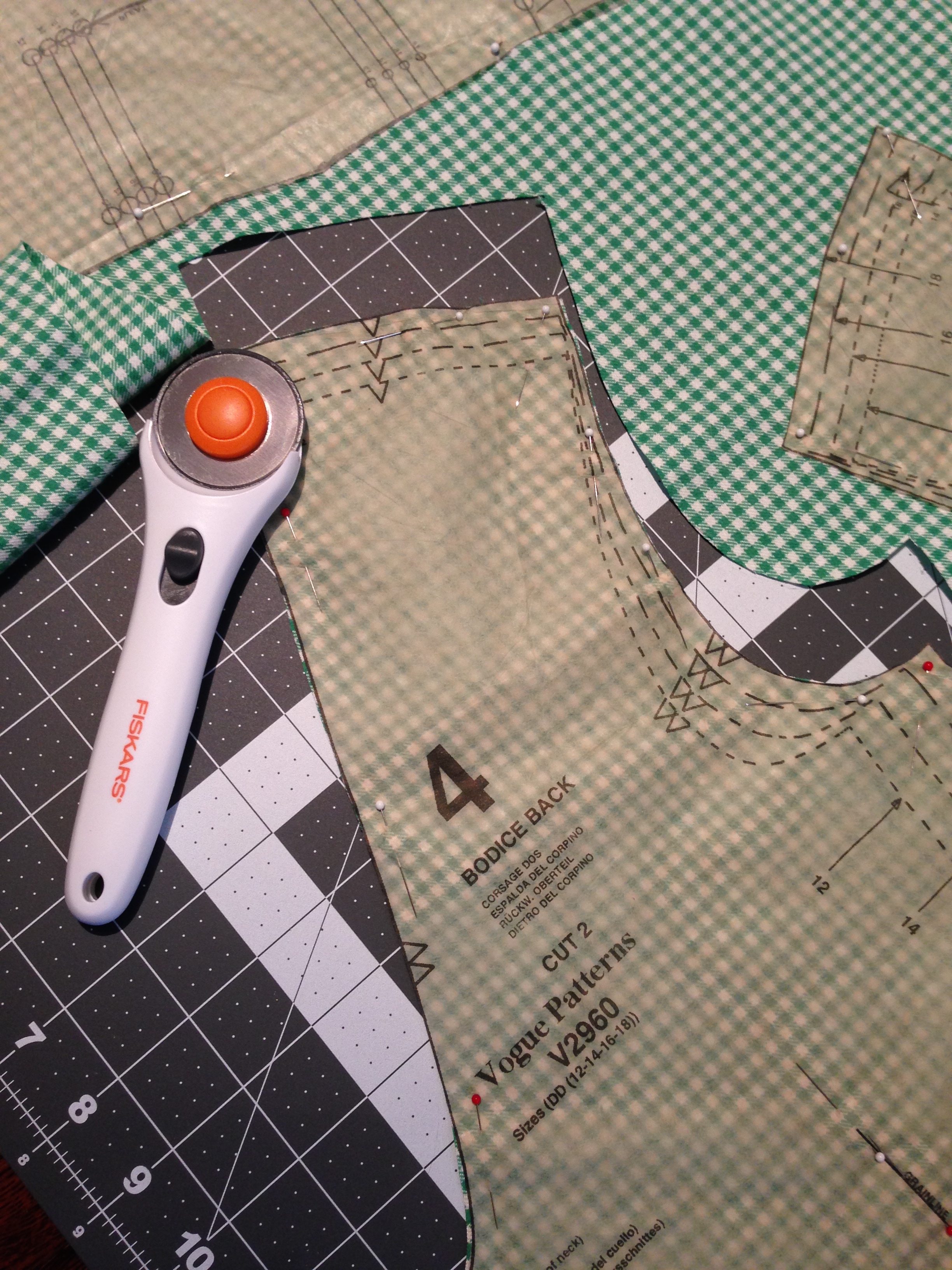
Step two, painstakingly iron and trace out the pattern. (Or be super lazy like me and just cut out the largest size and save all the little pattern remnants in a plastic baggy...>>.)
Next, organize the pattern pieces to fit on the fabric. Pin the straight of grain and then realize that in order to make sure the gingham isn't crooked you have to individually cut out every piece, so unpin every piece, unfold the fabric and start again.
Then go buy a rotary cutter and mat and shake a fist at Past Andrea for not doing this sooner. Cut out all the pieces! Making sure to mark all the little triangle bumpies with a contrasting thread.
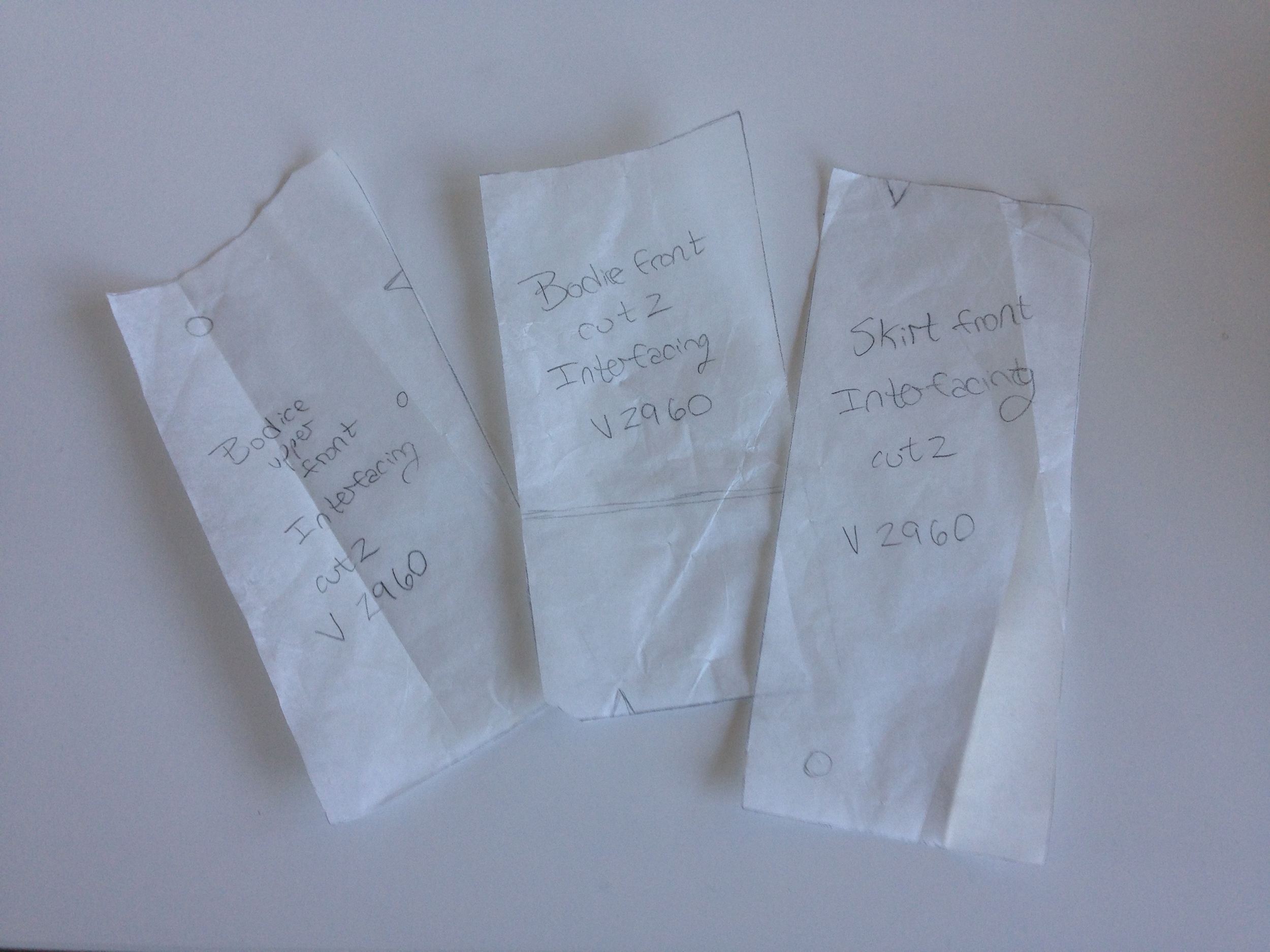
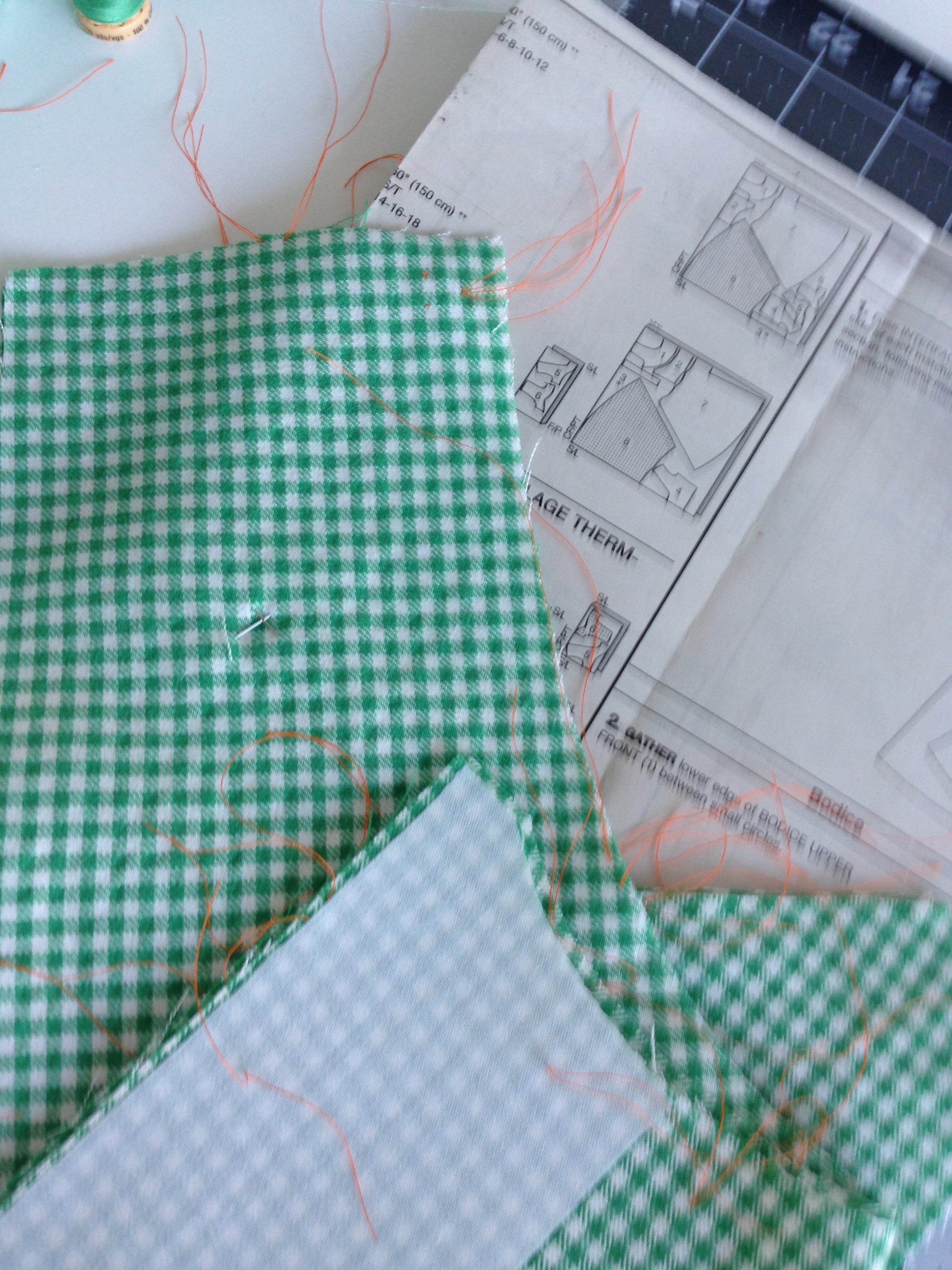
Now it's sewing time! Or wait! Interfacing is a thing that this lovely vogue pattern let's you make your very own pattern pieces for! How nice.
Phew. Ok. All interfaced. Time to start sewing!
Or maybe I'll just take another, very short, breather...
Stay Tuned!!
-Andrea
The Half-Assed Hobbyist